Filigrane Dichtungen - unverzichtbare C-Teile
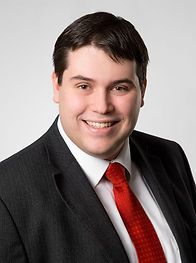
Mit dem Begriff Dichtung bringt man zumeist und vor allem einfache runde, ovale oder rahmenartige Fertigteile aus Faserstoffen oder Elastomeren in handlichen Abmessungen in Verbindung. In dieser Form sind sie geläufig und jeder hat sie schon einmal gesehen. Interessant wird es, wenn die Anforderung an eine Dichtung von den geläufigen abweichen. Diese Abweichungen können sich z.B. auf besondere Anforderungen an das Material, aber auch auf die Form und Größe der Dichtung beziehen.
Speziell filigrane Dichtungen faszinieren in Form, Fertigung und Anwendung.
Von Stephan Eifler – Theodor Winkel GmbH
Entwicklung filigraner Dichtungen
Moderne Technik wird immer kompakter, was zur Folge hat, dass auch die Träger technischer Komponenten immer kleiner werden. Zum Beispiel entwickeln sich elektronische Bauteile und Prüfvorrichtungen mit kleinen Kanälen und Speichern zu immer minimaleren Bauformen.
Die Reduzierung der Größe solcher Bauteile führt natürlich dazu, dass auch die Dichtflächen kleiner ausgelegt werden.
Bei der Planung eines Produktes, bei dem filigrane Dichtungen zum Einsatz kommen, steht die Dichtung als C-Teil zunächst nur selten im Focus und rückt erst in diesen, wenn es um die Umsetzung von Prototypen geht. Mit dieser treten dann auch die ersten Schwierigkeiten auf. Die Tatsache, dass auf eine filigrane Dichtung teils enorme Belastungen wirken, wird vorab gern außer Acht gelassen. Mit einem Querschnitt von z.B. 0,35mm² muss eine Dichtung dennoch diversen Anforderungen wie Druck, Langlebigkeit, Medien- und Temperaturbeständigkeit gerecht werden.
Eine optimale Order an den Produzenten zur Bestimmung des geeigneten Materials, enthält neben einer bemaßten Zeichnung (am besten DXF-Files) auch die vollständigen Angaben zu Toleranzen, Flächenpressung und Einsatzbedingungen. Werden bei der Anfrage wichtige Angaben vergessen, so kann dies bei der Bestimmung des geeigneten Werkstoffes natürlich zu falschen Resultaten führen. Wichtig für den Produzenten ist es alle Einsatzbedingungen in Hinblick auf die Belastung der Dichtung zu kennen. Schwankende Temperaturen, extreme Kälte- und Hitzespitzen und starke thermische Dauerbelastung sind nur ein kleiner Teil der Faktoren, die Beachtung finden müssen. Stoffe, die mit der Dichtung in Berührung kommen oder es könnten müssen genau so berücksichtigt werden wie der Druck und evtl. Zusatzanforderungen an z.B. die Langlebigkeit. Angaben über Toleranzen und Oberflächenbeschaffenheit vom Werkstück können auch wichtige Faktoren für den Entscheidungsprozess darstellen. Beispielsweise kann virginales PTFE bei engen Toleranzen, auf Grund des Kaltflusses, nicht eingesetzt werden und es muss in solchen Fällen auf ein modifiziertes PTFE zurückgegriffen werden.
Verfügt der Produzent über alle notwendigen Angaben, setzt er diese in Verbindung und ermittelt das Material, welches für den Einsatzzweck am besten geeignet ist.
Nicht für jeden Einsatzfall kann die optimale Dichtung ermittelt werden. Dies kann an vagen, bzw. unvollständigen, Angaben aber auch an zu vorsichtig definierten Anforderungen liegen. In solchen Fällen werden verschiedene Materialien zur Erprobung angeboten und als Materialmuster oder fertige Musterdichtung geliefert, die in Belastungstests unter einsatzähnlichen Bedingungen oder sogar direkt in einem Prototypen auf Tauglichkeit untersucht werden. Die Interpretation der Testresultate übernimmt i.d.R. der Kunde, wobei der Produzent, besonders bei schwierigen Fällen, gern mit einbezogen wird. Wenn sich lange Testreihen und Versuche für einen Kunden nicht lohnen (finanziell, zeitlich, zu geringe Relevanz, etc.), dann wird nach Haptik, Optik und Datenblatt entschieden.
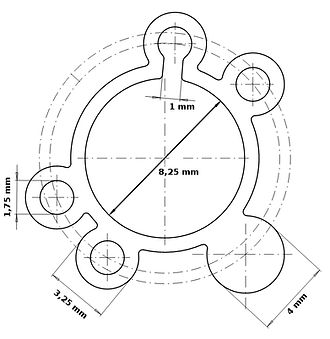
Prototypen und Kleinserien
Gängige Fertigungsverfahren für filigrane Dichtungen sind z.B. Spritz- und Gussteile aus Formen. Diese gewähren gleichbleibende Toleranzen und bei Massenproduktion eine kostengünstige Fertigung. Gerade bei filigranen Dichtungen ist es wichtig, dass Toleranzen eingehalten werden und eine saubere Verarbeitung stattfindet. Abweichungen in den Abmessungen, unsaubere Kanten und Schwachstellen im Material können schnell zu einem Ausfall führen.
In der Vergangenheit war die Fertigung von Prototypen sehr kosten- und zeitintensiv, da entweder teure Werkzeuge/Formen gebaut oder ungenaue Handfertigungen vorgenommen werden mussten. Kam es dann anschließend im Entwicklungsprozess noch zu Änderungen, so mussten Werkzeuge/Formen umgebaut oder gar neu angefertigt werden.

Um Kosten und Zeitaufwand bei Prototypen, Klein- und Mittelserien zu sparen muss man sich nach anderen Fertigungsmethoden umsehen. Eine der wohl vielversprechendsten, für diesen Einsatzzweck, ist die Wasserstrahl-Technologie (kurz WST), welche sich in den letzten zwei Jahrzehnten stetig weiterentwickelt hat.
Bei der Firma WST Winkel setzt man schon seit über 20 Jahren auf die WS-Technologie. Neben der WST kommen auch Plotter, Stanzen und Handarbeit zum Einsatz, aber auch Formteile können realisiert werden. Für den Prototypenbau und Kleinserienfertigung bei filigranen Dichtungen kommt, dank der genannten Vorteile, oft die Wasserstrahlschneid zum Einsatz.
Die Vorteile der WST sind vielseitig, so können bei richtiger Anwendung sehr saubere Schnittergebnisse erzielt und, je nach Material und Schnittbild, enge Toleranzen von bis zu wenigen Zehntelmillimetern realisiert werden. Da ein kalter Schnitt stattfindet, kommt es zu keinen thermischen Einflüssen, die Struktur und Beschaffenheit des Materials negativ beeinflussen könnten. Der sicherlich größte Vorteil liegt aber bei der Flexibilität! Da die WST-Methode auf Formen und Werkzeuge verzichten kann und lediglich ein CAD-Programm für die WS-Maschine geschrieben werden muss, sind die Kosten sehr gering und die Lieferzeiten sehr kurz. Sollten sich Änderungen ergeben, so können diese schnell und mit nur geringem Kostenaufwand vom Produzenten umgesetzt werden.
Bei der Produktion mit Formen muss für viele Werkstoffe eine eigene Form angefertigt werden, da der Fertigungsprozess auf die Eigenschaften des Materials abgestimmt werden muss. Bei der Fertigung mit WST muss weit weniger beachtet werden und es können mit einem WS-Programm verschiedenste Werkstoffe verarbeitet werden. Es ist für den Kunden somit möglich, mit geringem Kostenaufwand, eine Vielzahl an Werkstoffen in die Entwicklung einfließen zu lassen.
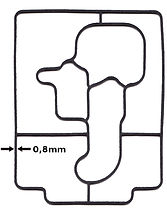
Die Grenzen bei filigranen Dichtungen
Je nach Kontur, Material und Einsatzzweck ist irgendwann bei allen Fertigungsverfahren die Grenze des machbaren erreicht. In diesen Fällen kommen meist Flüssigdichtstoffe oder auch Beschichtungen zum Einsatz.
Besonders bei Faserstoffen und Laminat-Materialien sind die Einsatz- und Verarbeitungsmöglichkeiten schnell ausgeschöpft.
Auf Grund der geringen Randbreite der Dichtung und der Materialbeschaffenheit kann es beim Fertigungsprozess zu Abplatzungen, Brüchen oder z.B. bei der Wasserstrahl-Schneide-Technologie zu Delaminierung der Schichten (z.B. bei Materialien mit Metalleinlage) kommen.
Serienproduktion von filigranen Dichtungen
Nach dem der richtige Werkstoff für die Dichtung festgelegt wurde und die endgültige Form der Dichtung feststeht, folgt die Serienfertigung. Auch dort steht man zunächst vor der Frage, welches Fertigungsverfahren gewählt werden soll.
Besonders bei Großserien liegt die Entscheidung für eine Fertigung mit Spritz-/Gussformen auf der Hand, da diese gleichbleibende Qualität und geringe Toleranzen versprechen. Durch hohe Stückzahlen amortisieren sich die hohen Formkosten in kürzester Zeit.
Wird hingegen aber eine geringe Stückzahl benötigt (z.B. <5.000 Stück) oder der Bedarf verteilt sich über einen langen Zeitraum, lohnt es sich auch andere Fertigungsmethoden für die Serienproduktion zu prüfen.
Auch bei zu erwartenden Änderungen im Serienprozess macht es eventuell Sinn sich einen anderen Weg als eine teure Form zu suchen, denn Formkosten können unter solchen Umständen schnell zu einem immensen Kostenfaktor werden.
Die Produktion mit WST (oder auch Plotter und Stanze, sofern möglich) kann also auch bei Großserienproduktion in Frage kommen. Zwar sind mit WST gefertigte Teile im Stückpreis teurer, dafür ist der Bau von Werkzeugen und Formen unnötig. Lediglich ein WS-Programm muss geschrieben werden, welches sich jederzeit und mit geringem Aufwand ändern und auf neue Anforderungen anpassen lässt.
Es ist letztendlich oft eine rein kalkulatorische Entscheidung in welcher Form die Serienfertigung erfolgt.
WST Winkel – der richtige Ansprechpartner
Nach nun mehr als 60 Jahren am Markt und mit fast einem Vierteljahrhundert Erfahrung im professionellen Wasserstrahlschneiden ist die Firma Winkel der richtige Ansprechpartner wenn es z.B. um die Realisierung von besonderen Dichtlösungen geht. Der große Maschinenpark (WST, Plotter, Stanzen, Spaltmaschine, Handarbeit), das umfangreiche Lager und die vielseitigen Erfahrungen und Fachkenntnisse der Angestellten sorgen für eine kompetente Beratung und Umsetzung von Kundenwünschen. Firma Winkel hilft bei der Entwicklung, dem Bau von Prototypen, der Produktion von Kleinserien und auch der Umsetzung von Mittel- bis Großserien. Weitere Informationen erhalten sie über die Homepage www.wst-winkel.de und www.facebook.com/WSTWinkel.
Theodor Winkel GmbH - Grovestr. 26 - 30853 Langenhagen
Telefon: 0511 / 72632-20 - Fax: 0511 / 72632-72 - Email: info@wst-winkel.de

Artikel wurde/wird veröffentlicht im:
"Technischer Handel" 2013 (VTH/Vincentz)
Jahrbuch "Dichtungstechnik" 2014 (ISGATEC®)
Bei Interesse an einer Veröffentlichung wenden Sie sich bitte an den Autor: s.eifler@wst-winkel.de